Когда речь идет об антикризисном управлении в автопроме, в качестве успешных примеров принято приводить вошедшие в учебники кейсы зарубежных производителей. Но такие практики есть и у нас: на протяжении нескольких лет, планомерно внедряя принципы своей производственной системы, «Группа ГАЗ» пишет собственную историю повышения производительности труда в условиях турбулентности. И у нее есть чему поучиться не только конкурентам: за счет универсальных инструментов из каждого кризиса ГАЗ выходит как минимум окрепшим технологически, как максимум — с новым продуктом.
Для всех отраслей российской промышленности в нынешнюю эпоху глобальных перемен есть несколько общих знаменателей: у всех возникла острая необходимость снижения затрат, многим потребовались способы срочной дозагрузки простаивающих мощностей, а значит, сохранения персонала, и, наконец, в большинстве сегментов экономики предприятия столкнулись с необходимостью импортозамещения и поиска новых поставщиков. Все эти вызовы за последние несколько лет в разное время вставали перед «Группой ГАЗ», и на каждый холдинг находил решения. Все инструменты основаны на принципах производственной системы, которая по дальновидной инициативе собственника ГАЗа Олега Дерипаски начала внедряться в структурах холдинга еще в начале 2000-х.
Внутренние ресурсы
Ключевым источником сокращения издержек в кризис становятся внутренние ресурсы компании, а способы повышения эффективности буквально ищутся в каждом цехе, на каждом этапе производства.
Во время мирового финансового кризиса 2008-2009 годов, который привел почти к двухкратному падению рынка коммерческого транспорта, перед ГАЗом стояла задача оптимизировать процессы на всех производственных площадках, в том числе в ООО «Нижегородские моторы». Директор по развитию производственной системы «Группы ГАЗ» Оксана Исакова вспоминает, что на тот момент на этом предприятии было несколько разрозненных производственных цехов, в каждом из которых вроде бы кипела жизнь, но анализ показал, что многие процессы дублируются, есть лишние уровни управления, большие запасы незавершенного производства и так далее.
Для ГАЗа это был один из ключевых проектов по производственной системе, которая в начале 2000-х началась с внедрения принципов Toyota Production System (TPS). «Это был сложный проект, разбитый на несколько этапов. Шаг за шагом были проанализированы все производственные процессы. В результате выстроили непрерывные потоки, начиная от заготовки и заканчивая сборкой и логистикой на главный конвейер, на производство грузовых автомобилей. На примере "Нижегородских моторов" нам удалось отработать схему внедрения TPS — от стандартизации рабочих мест до выстраивания непрерывного потока изделий», — рассказывает Оксана Исакова. Результаты впечатлили самих сотрудников: например, за счет оптимизации все потоки удалось выстроить в одном корпусе и в итоге высвободить три других, а это 70 тысяч квадратных метров площадей — существенная экономия на содержании основных фондов. Экономический эффект от этого проекта составил тогда порядка 80 миллионов рублей.
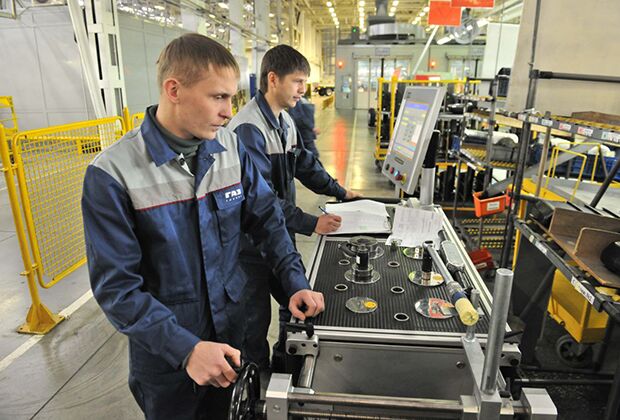
Фото: Михаил Сорокин
Опыт сжатия производств пригодился в 2010-2011 годах, когда в рамках партнерства с германским концерном Daimler потребовалось организовать контрактную сборку коммерческих фургонов Mercedes-Benz Sprinter Classic. Производство процесса подготовки кузовов новых машин под окраску решено было организовать на площадях прессового цеха №1 прессово-рамного производства. Для этого необходимо было освободить площади и перенести оборудование и детали в цех крупной штамповки, где в свою очередь предстояло сначала оптимизировать потоки, а затем перенести туда часть многотонного оборудования из прессового цеха в соседнем корпусе, причем так, чтобы не тормозить главный конвейер. «Сначала было страшно. Но когда начинаешь работать с командой, некогда бояться — надо просто делать. Мы понимали, что за нами стоит главный конвейер, надо все сделать в срок и не подвести», — рассказывает Оксана Исакова.
Работали творчески: специально созданная группа разрабатывала планировку сначала на бумаге — специалисты буквально вырезали модели оборудования и в масштабе расставляли их на схеме, чтобы минимизировать все затраты еще на стадии проработки. «Мы не могли потерять ни одного дня. На время работ по переносу создавался определенный запас изделий, но ровно на тот период, когда оборудование физически перемещалось и подключалось на новом месте. Точно в определенные сроки новое оборудование должно было запуститься и начать подавать детали», — говорит Оксана Исакова. В итоге за счет переналадки удалось закрепить за одним прессом вместо 10 изначальных 20 деталей, снизить время переналадки на крупных прессах с 54 минут до 14, а на линии мелких прессов — до 3,5 минуты. Чаще подаешь детали — увеличивается оборачиваемость, это позволило снизить запасы с 3,6 дня до двух. В результате общий эффект от реализации проекта превысил 47 миллионов рублей.
В 2020 году, когда ГАЗ, в отличие от многих российских компаний, уже был под санкциями США, Daimler свернул сборку своих фургонов на площадях ГАЗа, но опыт не «свернешь» — все наработки и компетенции остались в Нижнем Новгороде. И через несколько лет после начала работы с Daimler снова применялись — на этот раз уже на подготовке запуска в серию нового поколения фургонов «Газель NEXT».
В одном потоке
В 2014 году, в условиях двукратного падения курса рубля и подорожавших в одночасье импортных комплектующих, ГАЗ сосредоточился на модернизации собственных линий — штамповочной и сварочной. Предстояло освоить выпуск у себя больше 230 единиц высокоточных штампов, заказанных в Южной Корее. И снова сжатие, переналадка: номенклатуру одной из линий удалось увеличить с 15 деталей до 24-х. Экономический эффект достиг 700 тысяч рублей.
Одновременно в цехе сварки цельнометаллических кузовов внедряли робототехнический комплекс. Точнее, сначала искали для него площади, анализируя весь поток и оценивая потенциал каждого накопителя, транспортера, манипулятора.
Нужно было построить процесс таким образом, чтобы впредь не создавать отдельных линий для каждого нового продукта, а в одном потоке варить кузова для разных модификаций машин. Действовали рационально: часть оборудования закупали, часть — использовали с предыдущих проектов, часть модернизировали. Все это позволило сэкономить более 1 миллиона рублей и в итоге заметно снизить себестоимость автомобиля для потребителя, внедрив при этом уровень качества и технологий на уровне западных аналогов.
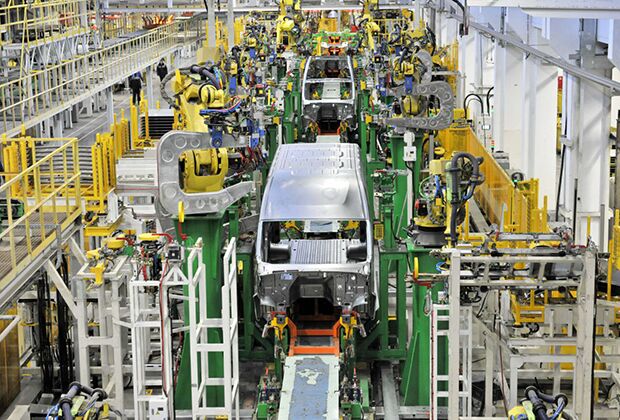
Фото: Михаил Сорокин
Подобные примеры рациональных подходов есть не только на площадке «Группы ГАЗ» в Нижнем Новгороде — инструменты производственной системы работают на всех предприятиях холдинга. Так, в 2017 году Павловский автобусный завод (Нижегородская область) осваивал новую модель газомоторной техники. Команда ПАЗа встраивала в основной поток сборку автобуса ПАЗ-32053 CNG. «Когда в 2017 году мы начали работать над первыми образцами, выяснилось, что из-за технологических ограничений сборка не укладывается в расчетное время такта конвейера, а это очень важно. Мешали и большая физическая нагрузка по грузоподъемности — вес одного только газового баллона составлял 75 килограммов, и многократное перекладывание деталей из-за отсутствия транспортировочной оснастки», — рассказывает Оксана Исакова. Снова помогли принципы производственной системы: оценив текущее состояние, механизировали процесс установки газобаллонного оборудования, организовали логистику. В итоге пропускная способность была увеличена с одного автобуса в смену до 10 без использования дополнительного персонала и сверхурочного времени. Кроме того, был внедрен принцип сборки разных модификаций в одном потоке. Экономический эффект составил порядка 3,5 миллиона рублей.
Мощная дозагрузка
В условиях снижения спроса неизбежно сокращение объемов производства, а это фактор риска для штатной численности. Смотреть по сторонам, изучать потребности рынка и других производителей, чтобы максимально загрузить простаивающие мощности — это главные рекомендации. «Еще год-два назад рынок труда не мог обеспечить все растущие производства, и с восстановлением экономики дефицит высококвалифицированных кадров снова будет очевиден. Поэтому надо всеми силами сохранять персонал, дозагружая мощности сторонними заказами, — говорит Оксана Исакова. — Кроме того, надо грамотно отслеживать свои запасы — ведь на какой-то момент это, по сути, замороженные деньги. Чем быстрее они оборачиваются, тем лучше для предприятия».
Для Завода автомобильных агрегатов «Группы ГАЗ» одним из таких заказов в 2013 году стал контракт с ООО «ПСМА Рус» (совместное предприятие Stellantis и Mitsubishi Motors Corporation в Калуге) на производство рам для автомобиля Mitsubishi Pajero Sport. Линия для этого проекта была организована с нуля, снова за счет внутреннего сжатия — переноса действующего оборудования и освобождения площадей: организовали новый участок сварки, установили новое оборудование фосфатирования и катафореза для антикоррозионной обработки деталей. Было создано 85 новых рабочих мест, и, хотя численность сотрудников увеличилась всего на 11 процентов, выработка на новом участке увеличилась на 40 процентов.
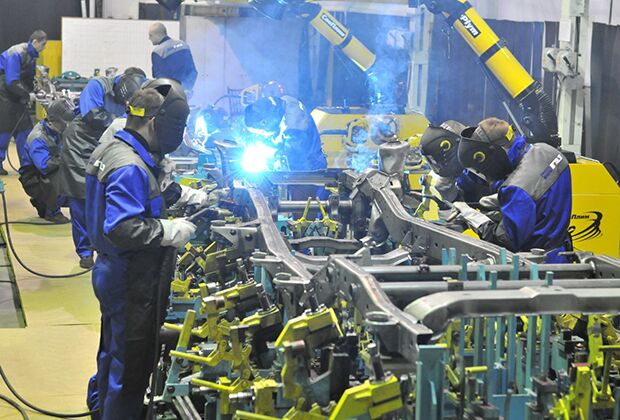
Фото: Михаил Сорокин
Совместное развитие
Пересмотр пула поставщиков в таких масштабах, как сейчас, для российских производителей, конечно, беспрецедентен, но, по сути, непрерывный поиск альтернативных партнеров для крупных компаний — привычная практика. В начале апреля «Группа ГАЗ» провела традиционный День поставщика, в котором приняли участие более 100 промышленных предприятий, представителей малого и среднего бизнеса Нижегородской области. «Вызовы сегодняшнего дня требуют ускоренного создания импортозамещающей базы на российских предприятиях. У "Группы ГАЗ" — свыше 3 тысяч российских поставщиков компонентов, материалов, оборудования. И для них сегодня открываются новые возможности. Мы находимся в диалоге с нашими партнерами в онлайн-режиме, показываем наши потребности и делимся опытом и компетенциями, наработанными на предприятиях холдинга», — сказал президент «Группы ГАЗ» Вадим Сорокин.
Диалог ГАЗа с партнерами, действительно, предусматривает не только обсуждение условий контрактов. Главный принцип закупочной политики холдинга: приобретать не конкретную деталь, а процесс ее производства — только так можно быть уверенными в стабильном качестве. Для этого ГАЗ готов делиться своим опытом организации бережливого производства, консультируя поставщиков непосредственно на их предприятиях. «Мы не можем позволить, чтобы наши партнеры стояли на месте: если они не меняются вместе с нами, если не реагируют на изменения на рынке, то мы как минимум каждый год сталкиваемся с удорожанием продукции от них», — поясняет Оксана Исакова.
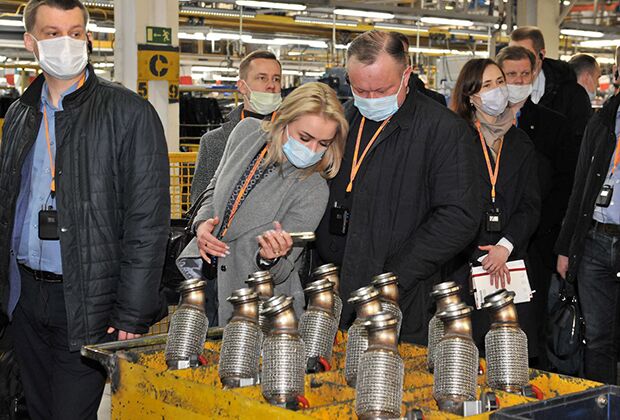
Фото: Михаил Сорокин
Одной из первых компаний, с которой «Группа ГАЗ» поделилась своей производственной философией, был завод, выпускавший для грузовиков ГАЗа бортовую фурнитуру. В 2015 году к качеству этой продукции у ГАЗа были вопросы. Специально созданная команда выехала на предприятие, проанализировала текущее состояние. Улучшения начались на потоке мехобработки картера. «Все началось с обучения: вместе с сотрудниками предприятия построили ячейку, где в единичном потоке изготавливали детали, а потом, через стандартизацию рабочих мест и операций, стали распространять опыт на другие участки. Когда объединили их в один поток, высвободили площади под другие проекты, — рассказывает Оксана Исакова. — В итоге в выигрыше остались все: поставщик смог оптимизировать процессы, улучшить качество и поднять зарплату рабочим, исключив текучку кадров. А мы, за счет сокращения себестоимости, в тот год получили снижение цен на компоненты на 2 процента».
Это не единственный пример — такое взаимодействие с поставщиками для ГАЗа системно — есть стратегия развития поставщиков, в рамках которой специалисты холдинга ежегодно выезжают на производства ключевых партнеров. «Мы никогда не отмахиваемся от наших поставщиков и их трудностей. Чем меньше проблем у них, тем меньше проблем у нас на сборочных конвейерах. Это единая цепочка», — заключает Оксана Исакова.
Большинство приведенных примеров — практики, реализованные ГАЗом за последние два десятилетия. Но они не теряют своей актуальности и сегодня, на новом витке экономических перемен. И дело не только в том, сколько средств команде ГАЗа удается таким образом сэкономить. Важно, что творческий подход стал привычным, каждодневным — это не разовые антикризисные меры: благодаря инициативе собственника, поменялось само мышление сотрудников, заточенное теперь на постоянные улучшения, а это главная гарантия конкурентоспособности и сохранения устойчивости во все времена. Кризисы меняются — опора на себя и собственные силы остается.